Aim
To introduction of the machine
1) anvil
iron block on which metal is placed to be shaped, originally by hand with a hammer. The blacksmith’s anvil is usually of wrought iron, but sometimes of cast iron, with a smooth working surface of hardened steel. A projecting conical beak, or horn, at one end is used for hammering curved pieces of metal.
The purpose of an anvil is to be the base workspace for forge welding and metalworking. Because of the multiple steps required during blacksmithing, such as hammering, cutting, and shaping, the individual compartments of the modern anvil contribute to creating a more accurate and high-quality weld.
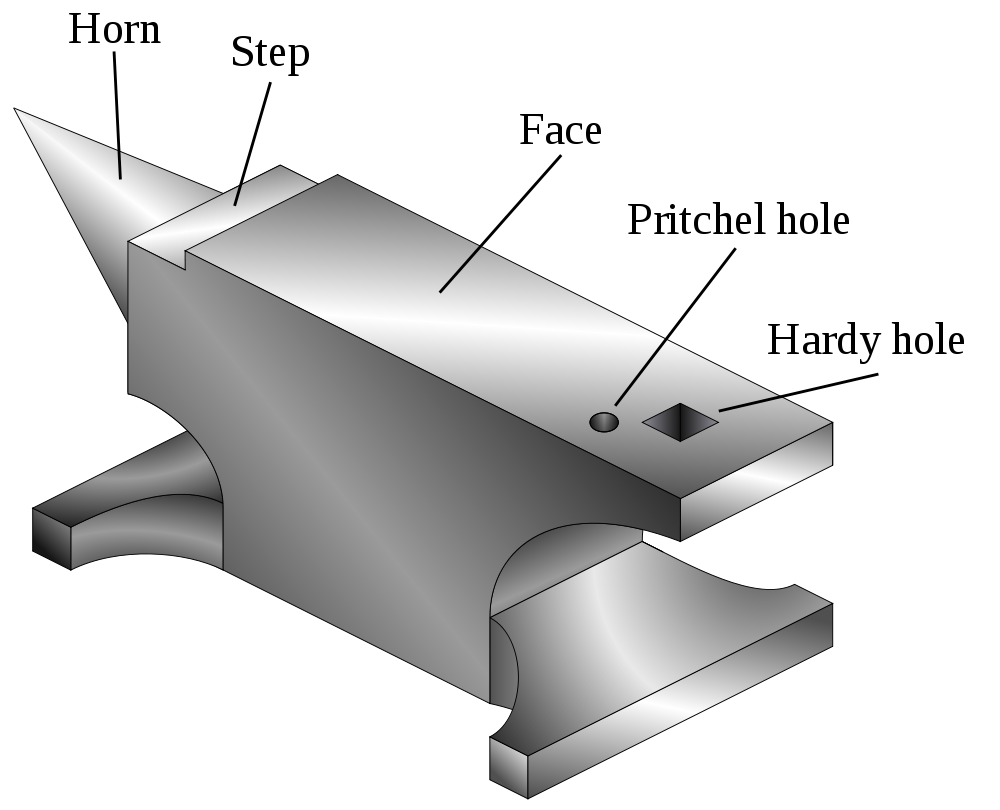
welding machine

Welding is a fabrication process that joins materials, usually metals or thermoplastics, by using high heat to melt the parts together and allowing them to cool, causing fusion. Welding is distinct from lower temperature techniques such as brazing and soldering, which do not melt the base metal.
Welding machines or welding guns or welders are among the most essential tools for a welding professional. Welding machines generate heat that melts metal parts, so that these parts can be joined. However, there is no single welding machine that is suitable for all welding projects.
A welding machine is a device used to join materials together. Welding machines produce heat that melts metal parts so that these parts can be joined. Thus, when it cools, it becomes a fixed and resistant joint. Different materials can be welded, although the welding machine generally works best with metals.19-Nov-2020
1. MIG – Gas Metal Arc Welding (GMAW)
MIG welding is a simple, popular form of welding, a novice can operate and master the art easily.
MIG stands for metal inert gas and sometimes may be called gas metal arc welding (GMAW). It is a semi automatic, quick process where filler wire fed through the gun and shielding gas expelled around to protect from environmental impurities. The filler wire fed on a spool to act as an electrode as well.

The tip of the wire acts as an electrode to create the arc with base metal which melts as filler material to create the weld. The process is continuous and requires presetting of the parameters as per the welding need. The versatile process to weld an extensive list of metals which produces a clean, smooth, and visually appealing weld bead.

These welding types are sensitive to external factors like rain, wind, and dust to make it not great for outdoor use. The quality problem with MIG welding includes dross and porosity to make the structure weak.
The commonest use of the MIG welding process is in automotive repair, construction, plumbing, robotics, and maritime industry. The welding offered is sturdy, strong, which can withstand enormous force.
2. Stick – Shielded Metal Arc Welding (SMAW)
These are century-old types of welding processes and improving regularly from time to time. It is popular welding because of its low cost, easy and simple operability. The process comes with spatter welding that needs clean up, essentially.

The filler material here is a replaceable stick electrode. It generates the arc when the end of the stick contacts the base metals. The heat of the arc melts the electrodes filler metal to make the weld. It coats the stick electrode with a flux that creates a shielding cloud to protect the weld zone from oxidation. The flux on cooling changes into slag, which needs to chip off.
The bright side of the process is that it is possible to perform the process of stick welding in outdoor and adverse weather like wind and rain. As it is possible to weld on rusted, painted, and dirty metals so it is useful in equipment repair. The variety of electrodes available in the market, but none work for thin metals. It requires long learning before you master the stick welding.
3. TIG – Gas Tungsten Arc Welding (GTAW)
TIG welding is possible with no filler material. The non-consumable tungsten electrode is used to create the arc when contacting the base metal. The strong arc melts the two metals and joins them. You may use filler wire if required. We need the constant supply of shielding gas to protect welding from the environmental impurities. It works better indoors and away from elements.

It is one the strong weld but difficult to master. Only an experienced welder can perform this art as they use both the hands in unison to perform the welding. The welding results are precise, strong, visually appealing, and require no cleanup. It is used to weld stainless steel, aluminum, magnesium, nickel, and copper with ease. The process is quite popular for industries that work on nonferrous metal as in tubing, bicycles, vehicle manufacturing. It is suitable to repair the tools made from aluminum, magnesium, and stainless steel.
What is TIG Welding?
4. Flux-cored arc welding (FCAW)
FCAW is similar to MIG welding, as the power source can perform both types of welding. MIG welding needs filler wire working as an electrode fed continuously from the gun. Conversely, FCAW has a wire with its core as flux and creates a gas shielding zone around the weld. No need for any external shielding gas in this welding type. The process is versatile and works for thick metals.

The welding process is efficient and works well for heavy metals with high heat welding. No need for any external gas makes it a choice of welding at a lower cost. It is useful for thicker metal and used in heavy equipment repair. Before you get a beautiful clean weld, you need to do cleanup from the slag of flux. It is done with ease outdoors as it does not require the shielding gas.
5. Submerged Arc Welding (SAW)

Type of welding involves the covering of metal pieces, welding wire, arc, and welding joint by a blanket of flux. It makes the process safe as there are no emissions of welding fumes, strong arc lights, and flying slags. The flux barrier protects the human and robot whosoever is performing the welding. It is a faster process for the high production industries.
SAW produces strong weld with deep penetration, with minimal preparation quickly and efficiently. It protects the welder from UV light and infrared radiation because of the flux layer.
6. Gas Welding/Oxyacetylene Welding

One of the hottest methods of welding at 3500 degrees celsius. The temperature of welding here reaches seven times hot as the biggest, hottest pizza oven. It generates heat when a mixture of fuel gases and oxygen passes in a torch. The process involves three types of flames: neutral flame, carburizing flame, and oxidizing flame.
The advantages of the welding process are many. It is portable because of pressurized gas filled in a handy steel cylinder. It is fairly easy to use, versatile for different sizes of metals. It is a very safe and economical option where a novice can perform easily.
7. Thermit Welding

When thermit (a mixture of aluminum powder and iron oxide) is ignited it leads to an exothermic reaction non-violent. The excessive heat melts the metal and pours at the needed joint surfaces. The liquid metal solidifies on cooling to create a solid welding joint.
It is a simple and fast method to join similar and dissimilar metal. This welding process does not need any power supply, only need is to heat the thermite at 1300 degrees celsius.
8. Forge Welding
What is welding? This is the oldest welding technique when we were questioning what welding is. This technique is answering for centuries. The metal here heated to a malleable state which hammered into the desired form and finally cooled to set in the shape.
The process came into mind while a blacksmith working on metal. It is not limited to these professionals only, but the forge welding happens to be a choice in the aerospace industry. The process needs a skilled user but a popular choice as there is no need for any filler metal.
9. Electron Beam Welding
Firing the ray of high-velocity electrons at the welding metal involves this type of welding. The energy from the electron transfers to the sheets to melt the welding metals, which can be joined and fused.
The type of welding is employed in multiple industries like automated automotive parts, and high-end aircraft engine industries. This can be a useful tool in aerospace components, bimetal saw blades, and transmission assemblies. It is a perfect choice to seal electrical components. The technique is good for dissimilar metals of various melting points and thermal conductivities. This welding method is good for thin and thick metal.
10. Atomic Hydrogen Welding
The welding process is replaced now by the MIG welding now in most indications. It is still a perfect choice for tungsten welding. This metal is heat resistant, but by this method, you can fuse without altering the metal when joining and welding them. They place the two metal tungsten electrodes in a hydrogen atmosphere. The hydrogen molecules in explosive heat can produce heat up to 3000 degrees celsius. The proper safety precautions like welder gloves, suits, goggles, helmets are essential.
11. Plasma Arc Welding
A newer technique developed in 1954 and similar to TIG welding. They pass the electrical current through an orifice of the nozzle protected by gases for the ultimate accuracy to weld a small area.It produces a narrow bead, pleasing weld, strong, and speedy welding.
The method used an extremely high temperature for a deep and stronger weld. The aircraft industry uses this technique, but not of any use for hobbyists and DIY users.
12. Resistance Welding

This is a thermoelectric process where electric resistance is employed to create heat, leading to a molten state of material to be joined. The efficient welding process which is pollution-free with minimum electricity consumption as well. It uses two electrodes in spot welding where the tip of the electrode produces heat and fusion on cooling. The following are the different types of welding.
- Spot welding
- Seam welding
- Projection Welding
- Flash butt welding
Finishing Words
We expect now, you have a basic understanding of the various types of welding. Few types are run by simple machines while others need expensive equipment. Some can be performed by DIYs and hobbyists without spending too much. Now is time to purchase a welder, check our guide to buy a welder.
Thank you for sparing time to read the article but your comment will help us to understand your need.
chaff cutter

A chaff cutter is a mechanical device for cutting straw, pipes ,roads, irons or hay into small pieces before being mixed together with other forage and fed to the horses
Welding Table
A welding table is a platform that is at waist level and it works like a workbench. You use it when you are working in metal fabrication with welding. A welding table is very useful because it gives the welder a stable place to work and also can provide assistance with both squaring and measuring.
Bench Grander machine
These types of grinders are commonly used to hand grind various cutting tools and perform other rough grinding. Depending on the bond and grade of the grinding wheel, it may be used for sharpeing cutting tools such as tool bits, drill bits, chisels, and gouges.
Essentially, bench grinders are just tools for spinning grindstones, and these grindstones are for gently shaping metal. They’re commonly used for getting blunt tools back to full sharpness, but they’re not a one-stop-shop for instantly putting an edge on a tool. When using a cutting blade, the edge gradually dulls.14-Sept-2018

CO2 gas welding
Pure CO2 provides very deep weld penetration, which is useful for welding thick material. However, it also produces a less stable arc and more spatter than when it is mixed with other gases. It is also limited to only the short circuit process.

pillar /bench drill machine
What are pillar & bench drills used for? Pillar & bench drills are used to create holes in a wide range of materials, from woods and plastics to metals.
Spot drill machine
Spotting drills create starter holes that help prevent drill bits from walking (or moving) when the hole is drilled deeper with a drill bit. Also known as hole-starting drill bits or spot drills, these short drill bits have a rigid shank that helps ensure the starter hole is accurate and has clean sides.
Bench voice
A bench vise is an essential and integral tool used in metalworking, woodworking, and some other manufacturing applications. It is mounted on workbenches and its main function is to hold the workpiece safely and securely.28-Jan-2021
Lathe machine
A lathe is a machining tool that is used primarily for shaping metal or wood. It works by rotating the workpiece around a stationary cutting tool. The main use is to remove unwanted parts of the material, leaving behind a nicely shaped workpiece.26-Jul-2020
Power hacksaw
A hacksaw is a type of hand tool designed specifically for cutting through materials such as plastic, steel, and other metals. They are a variant of the traditional hand saw, typically used for cutting wood, and have become a staple tool for professionals and hobbyists alike.
Milling machine
Milling machines are very versatile. They are usually used to machine flat surfaces, but can also produce irregular surfaces. They can also be used to drill, bore, cut gears, and produce slots. … A milling machine removes metal by rotating a multi-toothed cutter that is fed into the moving work piece.15-Jul-2016
A milling machine removes material from a work piece by rotating a cutting tool (cutter) and moving it into the work piece. Milling machines, either vertical or hori- zontal, are usually used to machine flat and irregularly shaped surfaces and can be used to drill, bore, and cut gears, threads, and slots.
Compressors
Compressors are used throughout industry to provide shop or instrument air; to power air tools, paint sprayers, and abrasive blast equipment; to phase shift refrigerants for air conditioning and refrigeration; to propel gas through pipelines; etc.
pipe roling machine
A rolling machine is a piece of manufacturing equipment that contains two or more rollers through which raw metal is fed. The purpose of rolling machines is to compress raw metal into a thinner and more uniform shape, which is essential when producing sheet metal.
Measurements
Aim : To understand the method of measurement
Requirement : metre tape,
british method : British method is using to declare the winner in a League tournament. in British method there are point system the team who won the match getting 2 points. and for losing getting 0 points on the terms by getting one points for each British Formula is total obtained.
Matrix method
vernier caliper :
Vernier calipers are measuring tools used mainly for measuring linear dimensions. These calipers come handy in measuring the diameter of circular objects. Their circular jaws fit securely on either side of the circumference of round objects.29-May-2019https://www.shakedeal.c
How to Use a Vernier Caliper
Definition of vernier caliper
: a measuring device that consists of a main scale with a fixed jaw and a sliding jaw with an attached vernier.
least count of vernier caliper = 0.02
kg/km | Hecto | deca | metre/gram/liter | Deci | Cemi | Mili |
WELDING
Aim
. To learn welding
Requirements:
Welding machine, Welding screen, measuring instruments, chipping hammer, rods, angles, welding rods etc.
Procedure:
1
Select the job for practical. Examples for jobs are given below You can
select any new itern as well
Sample list
. Fabrication of simple furniture for home or school, rack, cot, table, chair. desk, blackboard and stand etc.
OR
Fabrication of simple farm equipment, such as harrow, weeding tool,
seed drill etc
OR
Fabrication of useful transport aids, wheel barrow, trolley, cycle trailer
etc.
Welding, straightening, drilling, cutting and grinding enough to make a strong weld, without burning of the metal, negligible spattering and continuous weld
2 Clean the joint to be welded
3 Connect earthling
4 Use welding goggles/screen/helmet. 5Practice striking are using welding rod
6 Do welding to connect two jobs
7Do the costing of the job done
Observation:
1 Draw flow chart(SLD)
2 Write precautions to be taken during welding
3 Write your experience of striking arc
4 Did you manage to judge the distance of welding rod and job through screen
5 Write down prices of welding rod, material available in the market.
6 The welding machine you used, is single phase or three phase? What is
the difference?
Conclusion:
What do you feel about the work you have done ? Write your comments. Did you enjoyed it ? Do you want to improve it? What went wrong? Any learning experience
Community service areas All fabrication jobs viz making windows, doors.
repair work etc
Precautions
1 Do not bend rod while fixing it on the holder.
2 Do not connect earthing and holder when machine switch is ON
- Do not change current when machine is ON. Do not strike arc without using screen
4
5 First strike a test spot and then carry out weld run 6. Do not chip hot job
7
Job should be clean using wire brush
Safety rules for arc welding:
Do not use machine getting prior knowledge about
electric connections checked from electric section
Use boots, hand gloves, hand screen for safety To remove welding deposits use chipping hammer
Use grinding goggle while chipping This will protect your eyes from in your eyes
6 7 Keep welding machine away from water. Depending on the job and its size (Thickness) Electrode dia and Current set eg thickness of MS 1/4″ (6mm) electrode gauge 10 (3.25mm) and
current 90-120 Amp
GI threading
Aim
to learn how to fall the thread to galvanise iron pipe
Requirement
GI pipe, die,
procedure
To take the GI pipe to get the fit to pipe vice.to bear the GI pipe tight to the hand.After fit on the die of GI pipe.next rotate the die and to throw the oil on it.
observation
it takes a lot of strength.
well, job to the earned money. .
INTRODUCTION TO CARPENTRY
introduction to carpentry
Info : carpentry means to cut, trim a wood piece into something desirable
for example we can cut wood pieces and modify them or convert them into a table
for carpentry vu many equipments like wild stone for sharpening hacksaw for cutting wood cutter for cutting and many more
in carpentry we learn how to make use and make L and E joints
right angle
it is used to measure corner of table box etc.
Coping saw it is used for cutting iron wood and plywood
G clamp it is used for stuck iron and wood
hand saw it is used for cutting wood and plywood
Measure tape it is used for measure the distance of between two points
clow hammer it is used for knock the nails and remove the nails.
dead blow hammer it is used for knock the nails and any other things
Chisel it is used for fall the hole
Sandpaper it is used to do smooth part wood and to remove the ganj
nails it is used for joint to the two-part.
Jack plane it is used for smooth part of wood
screwdriver it is used for set the screw
woodcutter it is used for cutting wood
Oilstone it is used for sharpen chisel, Jack plane blade and wakas
kikre it is used for draw the design and to hold the small hole of wood.
diwad pliyer It is use to doing diwad for the teeth of hands saw.
round file it is used for rub the hole of Steel plate iron plate
triangle file it is used for sharpen the teeth of hand saw
half file it is used to rub the hub hole of iron plate
hand drill it is used for fall hole on the wood
Sharpen to the carpenter tools
Aim. to sharpen the carpenter tools
Requirement
hand saw ,triangle file ,chisel ,oil stone, Jack plane bled etc.
How to sharpen a saw? Saw and packed in bench vice .Then triangle file ne
INTRODUCTION TO EQUIPMENTS
measurement tape: this is used to measure and mark onto something
hand grinder machine: and brand machine are angle grinder is used to cut polish and trim some metal pieces
chop Saw Machine: chop saw machine is used to cut big pieces of metal at resize 90 degree 45 degree 30 degree 60 degree
Lathe machine: Lathe machine is used to drill specific areas in a cylindrical bar of specific diameter and design it in a specific way to do some task
spot welder: spot welding machine is used to spot weld thin iron sheets together
bench grinder machine: bench grinder is used to sharpen blade of some equipments and also train some ages of material
bench vice: bench vice is used to hold onto something
welding machine: welding machine is used to weld two metal pieces together
FUNNEL
Aim: to make a funnel using iron sheet
Requirement: iron sheet ,Snipper ,marker ,measurement tape
Procedure:1) mark the lines as shown in in the below diagram and cut it using slipper
2) fold along the dotted lines
3) and cut along the straight lines.
———————————————————————————–
CONCRETE BRICKS
AIM : to make concrete bricks
REQUIREMENTS : sand , cement , water ,mould for bricks
PROCEDURE : volume of brick = l*b*h
= 0.85*0.14**0.17
= 0.00826 cubic meters
mix cement, water , and sand in proportions gives above . put the mixture in the brick making mould or put it in the bricks making mould or put it in the brick making machine .Adjust the mortar in the mould and then compress it remove it from the mould and leave it to set
PAINTING
AIM : to paint onto an object
requirements paint, object to paint, painting brush, thinner,
Procedure: 1) first clean the area on which we have to paint
2) then proceed to paint using paint brush while painting make sure that you apply a thin layer of paint on to the object
3) after painting is done leave it to set for a day
4) after painting is done clean the brush using thinner that is the Penta lawyer
DIFFENT TYPES OF HINGE
AIM: to learn about different types of hinge joints
- Parliament hinge: this is used for big doors
- hinge this is used for heavy dose
- strip hinge this is used for following doors
- piano hinge this is used for big doors
screw types : 1) height of screen
2) clip top screw
3)square tops group
4) flat top screw
TO FIX SUNMICA ON THE WOODEN BOX
AIM : To fix Sunmica on the wooden box
requirements Sunmica, Sunmica cutter, Teri call, cello tape
Procedure: 1) cut Sunmica of appropriate length using Sunmica cutter
2) use Fevicol to stick the Sunmica on the board
3) hold the Sunmica in place using Sun or tape
4) leave it to set for one day
L&T JOINTS
aim to make L&T joints
L shaped holders: during the construction of wooden box Using some tools we create l shaped holders this holders can be measured whether they are at right angle using set squares
t shaped holders: why using the equipments used in carpentry it’s possible to create t shaped holders
TO BUILD A FOUNDATION OF A BUILDING
Aim : to build a foundation of a building
Requirements: limestone powder for marking, nylon rope, iron rod, measuring tape,
procedure:1) first measure the appropriate measurement from the side of the road 8 feet in in our case
2) then mark using a rod at four points and at right angles put 3 moulds at appropriate distance
3) then mark the exterior line using limestone marker
4)then around 6 inches inside draw a line and continue it 5 more Times
5)the first two strips are exterior foundation and 20
6) the in
7)the middle strip is the area to lay bricks
FERROUS CEMENT SHEET
aim ; to make ferrous cement sheet plastering and to plaster manhole over
Requirement: Cement , sand , chicken mesh , weld mesh , welding rods,
Procedure : 1)
First make an L – angle using iron rods by cutting them at certain angles
2)then weld the angles together using welding machine
3)then weld the weld mesh to the angles using welding machine and welding rods
4)After completing it secure the chicken mesh to the contraction using small tar
5)Make cement mortar in proportion 1:3 cement : sand to make Ferros cement
6)Spread gunny bag something down and then place above the recently made mesh
7)Fill it up with ferrous cement and level it
8)Leave it to set and continue with curing process for 3 days until it hardens
THREADING
Requipements : 10mm rod , 10 mm die , coolant
Procedure:
- At start 10 mm rod is required
- Fix the 10 mm rod in the bench vise
- Fix the 10 mm DIE in the DIE holder
- Slowely turn the die / fix it inside the box
- Follow the rule of two clockwise rotation and one anticlockwise rotatio
- Use coolant to increase the efficiency of the threading and to increase the life of the DIE
After threading completed spin the DIE one more time so as to confirm that the threading has been done properly
SAFETY RULES
1) workshop should be kept clean
2) whenever working in a workshop necessary rules must be followed with utmot dilegency
3) whenever working in a workshop necessary safety equipements must be used
4) safety gloves is a must whenever grinding or welding
5) safety gloves and apron should be used whenever grinding
6) to hold hot equipements a rod and heat resistant safety gloves must be used
7) To protect eyes safety glasses must be used
8) whenever a machine is running do not get distracted
9) in case of fire to douse it fire extinguisher must be used
10) while using a machine if any risk arises then stop the machine
11) In workshop plenty of ventelation must be there
12) in workshop there should not be spillage of any oil if spilled then clean it immediately
13) eqipeme nts must be kept from where they are taken 14) In workshop no one should fight and ones beheaviour should not be troublesome
SOLDERING
AIM : to learn soldering with soldering metals and khadya
REQUIREMENTS ; khadya, solder metal, a object to solder
PROCE3DURE: 1) first heat the the khadya
2) clean t5hye surface to be soldered with ZNCL whichj is made by mixing HCL
3) clkea n the are to be soldered with wirer bruysh
4)after the khadya is heated up apply it to the part to be soldered and mealt the solder material and apply it to the material to be soldered
TAPPING
AIM : to make thre4ads in a nutbolt
REQUIREMENTS: tapping bit , metal plate, coolant
procedure: 1) at start take metal piece
2) center punch the hole you want to make
3) drill holes in it
4) holes should be of less as much of the pitch diameter of the tap you want to make
5) drill hole through
6) start tappin g through it usingf tappinmg bit
7) while doing it follow the rule of 2 clockwise rotation and 1 anticlockwise rotation to minimize damage of the nut
TO SHARPEN SOME EQUIPEMENTS USED IN CARPENTRY
AIM : To sharpen some equipements used in carpentry
Requirement: wildstone, divad pakad,
Info :
Wildstone: this is used to sharpen some equipments used in carpentry
Saw ; we use it to cut wooden items
Divad pakad : this type of equipemen is used to give sharpeness to the gear
Procedure :
- We use wildestone to sharpen equipemnts used in carpentry
- Use divad pakad to a straighten the bent teeths on the divad pakad
TO LEARN DIFFERENT TYPES OF ARRANGEMENTS OF BRICKS
AIM : to learn different types of arrangements of bricks
ENGLISH BOND : in this type of bond streacher and header side of bricks are arranged alternatively on top of each other and queen closeure is added for the subdivision
FLEMISH BOND : in this type of bond two streacher and a header bond is arranged on top of each other
STREACHER BOND : in this type of bond bricks are layed such that streacher side is viewed from front side this type of construction generates a 4 inch thick wall
HEADER BOND : in this type of bond bricks are layas there such that header side is viewed from front side this type of construction generates a 9 inch thick wall
RAT – TRAP BOND : Flemish bond when turned upright it becomes a rat trap bond this type of bond is the most efficient type of bond as there is a insulation oif air in between the two bricks when one side is hot hen the other side is cool and vice versa as is a cavity in between the two bricks less material is used so it is also pocket friendly
AIM : TO MAKE A RCC COLUMN
Requirements : holding structure for the concrete column , pickaxe , Cement , Sand , Stones , Water , Some wire
Procedure : 1) first of all make normal mortar by mixing Cement: Sand : Stones in the ratio 1 :3 : 3
2) erect the iron rods in the foundation beforehand
3) make a contraption to hold the mortar
4)secure the contraption onto the iron rod
5) pour the concrete in it from above and constantly vibrate or move it so that the mortar can settle below